We use education and capacity building – not enforcement – to make safety inherent to factory operations in Bangladesh.
Our Theory of Change
To create and sustain the change we seek – a culture of safety in Bangladesh factories – we conduct programming that promotes worker safety, provide a forum for members to collaborate and engage with each other, and advocate for effective workplace-safety policy.
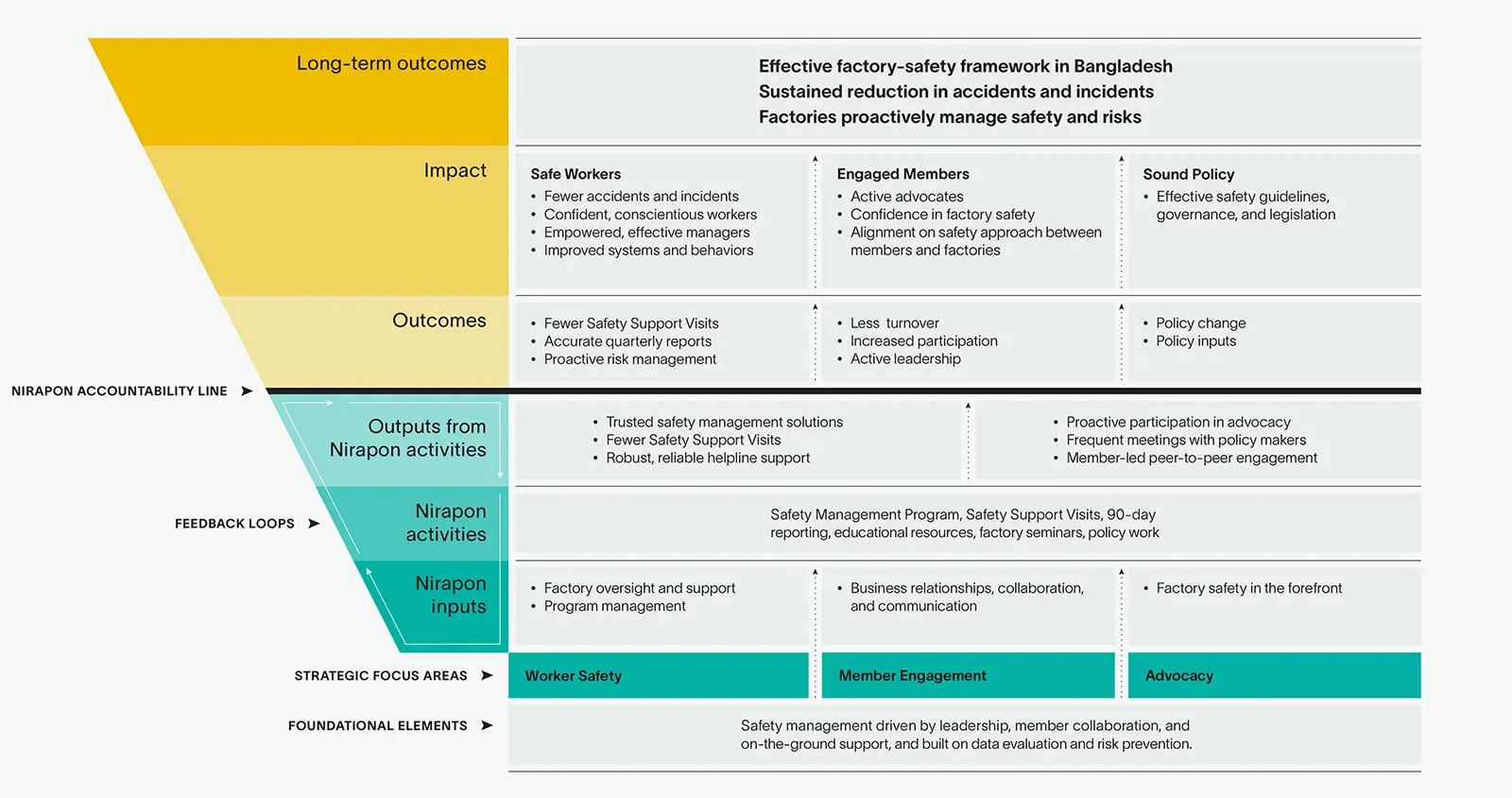
Our Services
Our member companies enroll their supplier factories in the Nirapon Safety Management Program, which delivers three interdependent services provided by our local partners. They bring technical expertise, accountability, and insights to our core operations.
Safety Systems
Our safety support team guides factories through a comprehensive, systems-based approach to safety management. This process, which includes factory reporting with fact based evidence and site visit, delivers tailored guidance to help factory managers gain a holistic view of their factory safety and establish effective safety management systems.
Educational Programming
Our safety implementation program complements our Safety Systems program by helping everyone inside the factory understand and uphold their role in creating a safe workplace. Through this program, we train managers and factory-based internal trainers and help factories establish their own administrative controls to develop and maintain a safe work environment.
Worker Helpline
We partner with Amader Kotha, an independent organization that operates an anonymous helpline that gives workers a direct voice to report safety and other issues, allowing managers to resolve these issues in a timely and sustainable way. We use helpline data as an early-warning system to identify emerging risks and patterns of behavior to inform our Educational Programming